As part of the High-Luminosity Large Hadron Collider (HL-LHC) upgrade, critical modifications are underway to enhance reliability and performance. The existing vacuum sector valves within the LHC tunnel will be removed and replaced by advanced VAX modules, strategically positioned inside the rotating shielding structures of the CMS and ATLAS detectors.
The installation posed a significant engineering challenge due to extremely limited space inside the shielding, risking potential damage to sensitive neighboring components during installation and maintenance activities. To overcome this, engineers precisely machined dedicated pockets into the shielding doors at both ends of the CMS cavern, ensuring adequate clearance for safe installation.
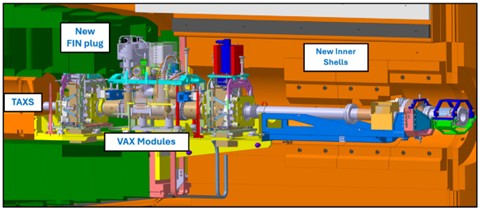
Additionally, two M16 threaded holes were incorporated into the design, enabling the installation of end-stop bumpers. These bumpers provide a crucial protective feature, limiting the travel of the shielding and preventing unintended contact with adjacent equipment.
The machining task was further complicated by restricted personnel access due to radiation hazards. To address these constraints, the BE-CEM group, in coordination with the HL-LHC Collider-Experiment Interface Work Package (WP8) and the CMS Experiment Systems group (EP-CMX), deployed a remotely operated robotic milling solution designed according to the ALARA (As Low As Reasonably Achievable) principle. This innovative solution significantly reduces radiation exposure for personnel and minimizes contamination risks associated with manual machining.
The robotic solution utilized a KUKA KR 120 industrial robot arm with six degrees of freedom and a payload capacity of 120 kg, equipped with customized and highly sensorized, air-cooled electro-spindle optimized for high-precision machining. To ensure accuracy and safety, the robot featured a digital contact sensor for precise localization and an inertial measurement unit (IMU) for real-time vibration monitoring during machining operations. Furthermore, the robot was enclosed in a protective cover to safeguard against contamination, highlighting CERN’s commitment to precision, safety, and innovation in preparing the LHC for future high-luminosity operations.
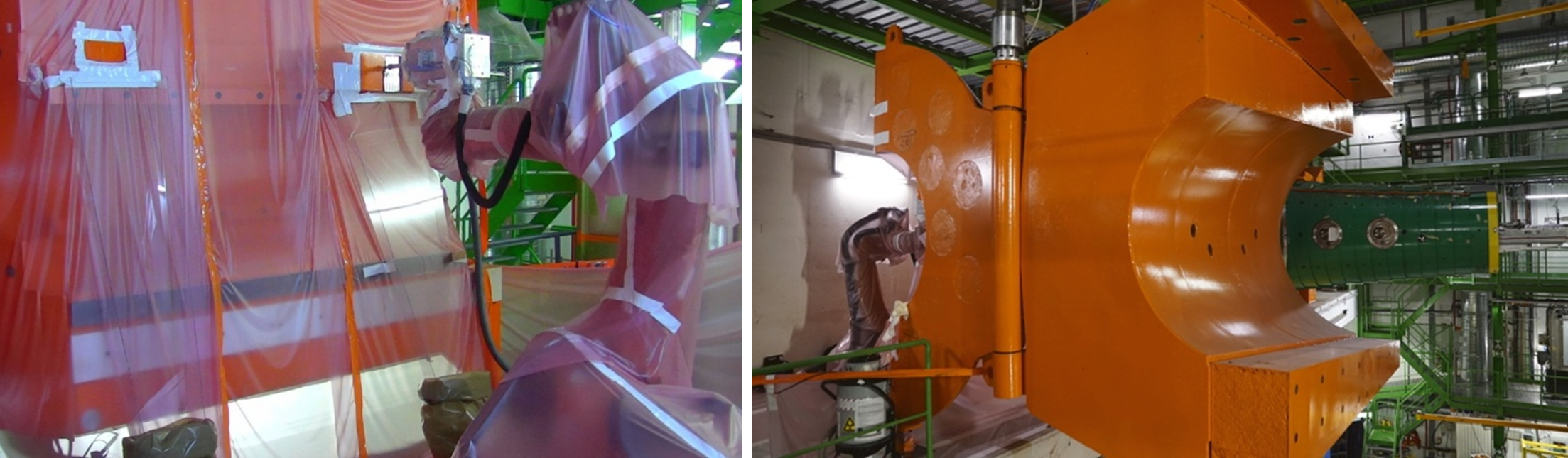
Engineers operated the robot from a remote control station positioned in a radiation-safe zone inside the CMS cavern, programming and supervising the precise machining of the internal parts of the shielding. Prior to physical intervention, the entire process was meticulously simulated in a virtual environment, confirming precision, feasibility, and safety. This comprehensive approach highlights CERN’s commitment to innovation and meticulous preparation for the LHC’s high-luminosity operations.
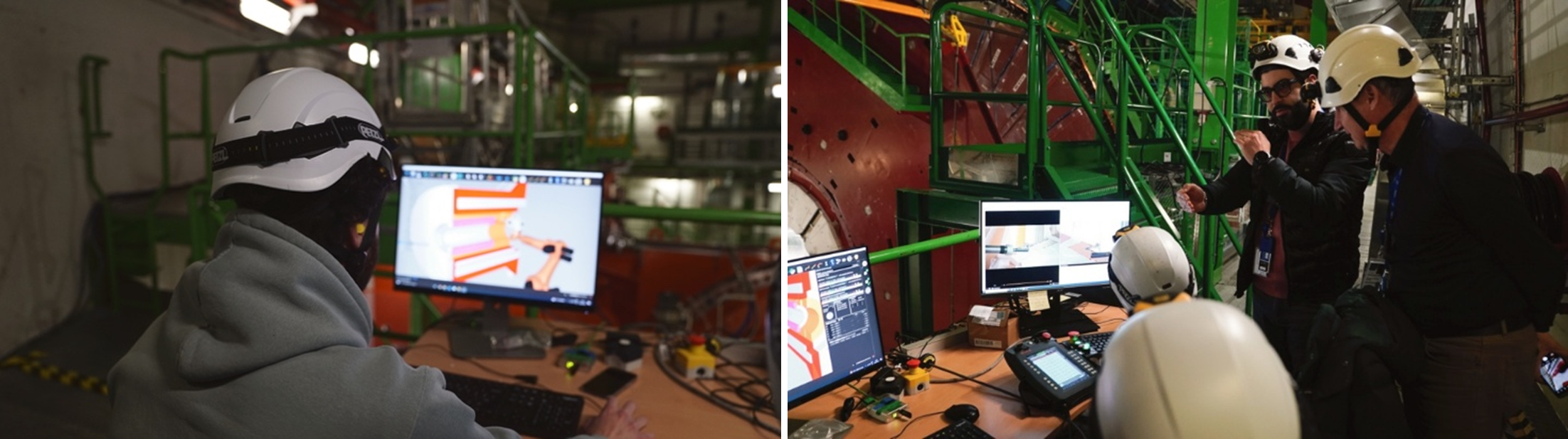
For pocket milling, the team employed a trochoidal milling technique, characterized by helicoidal tool motions, optimizing material removal rates and minimizing cutting forces and tool vibrations. This approach allowed stable cuts up to 15 mm deep. Threaded holes were machined using a two-step process: first drilling pre-holes, then threading via helical ramping. The machining process was specifically optimized for dry conditions, effectively limiting contamination spread.
By leveraging this advanced robotic solution, the BE-CEM team successfully minimized radiation exposure, reduced contamination risks, and prevented potential damage to sensitive components. With the robotic intervention now complete, the CMS shielding is fully prepared for LS3 and ready to receive the new VAX sector valves, marking a significant advancement in the HL-LHC upgrade project.